Software path optimization made quick instrument servo m
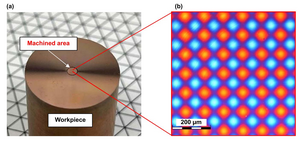
[ad_1]
The researchers in Keio College developed a novel instrument path technology technique for driving an independently managed quick instrument servo (FTS) for freeform floor machining. With out necessity of trial and error, the tactic permits fast manufacturing of high-precision freeform optics.
The instrument path program was generated utilizing the ring and mesh strategies as a substitute of the traditional spiral instrument path. The instrument path was optimized by analyzing the impact of interpolation error utilizing type error prediction. The optimization of management factors format consists of two steps. Initially, the variety of management factors is decided. Then, the optimum facet ratio of the format parameters is decided. Experimental validation by machining two-dimensional sinusoidal waves and micro-lens array demonstrated the effectiveness of the instrument path optimization technique proposed on this examine. The proposed technique lowered the form error from submicron to 10 nm stage for two-dimensional sinewave.
Professor Jiwang Yan commented, “FTS-based diamond turning is a tremendous technique to manufacture freeform surfaces with excessive effectivity, however typical FTS items pushed by piezoelectric actuators have very small strokes in micrometer scale, limiting their purposes. Lately, long-stroke FTS items, geared up with voice coil pushed air bearings, have been developed, which allow millimeter-level working strokes, and in flip, significantly expands the purposes of FTS diamond turning. To enhance the system compatibility and stability, these voice coil-based FTS items are independently pushed by separate management techniques. Nevertheless, the instrument path technology technique for such FTS has not been established but, which is considered a bottleneck”.
The researcher, Mr. Yusuke Sato mentioned, “This examine goals at proposing novel strategies to producing and optimizing the instrument path for the unbiased FTS management system to cut back type error of a machined floor attributable to two-dimensional interpolation. Firstly, management level clouds are pre-generated in two totally different strategies, specifically, ring technique and mesh technique. Based mostly on the distribution of the management factors, the ultimate machined floor profile is predicted and interpolated by simulation. Then, by evaluating the simulated floor with the designed floor, the shape error is obtained. By repetitively adjusting the parameters of the management factors, the shape error was minimized to the specified tolerance”.
This examine establishes an necessary base for additional growing ultraprecision machining applied sciences of freeform optics via diamond turning through the use of a FTS unit with a separate controller to realize excessive accuracy with out necessity of trial and error, which contribute to superior manufacturing of excessive value-added merchandise.
Professor Jiwang Yan mentioned, “The developed instrument path technology/optimization system makes the commercially accessible FTS items extra exact and highly effective. It’s particularly helpful to enhance the productiveness of freeform optics that are broadly employed in varied merchandise comparable to VR/AR techniques, cameras, scanners, head-mounted shows, and elements utilized in aerospace and biomedical engineering. Fast manufacturing of such freeform surfaces could change the ideas of product design within the close to future.”
About IJEM:
Worldwide Journal of Excessive Manufacturing (IF: 10.036) is a brand new multidisciplinary, double-anonymous peer-reviewed and absolutely open entry journal uniquely masking the areas associated to excessive manufacturing. The journal is dedicated to publishing unique articles and critiques of the best high quality and influence within the areas associated to excessive manufacturing, starting from fundamentals to course of, measurement and techniques, in addition to supplies, buildings and gadgets with excessive functionalities.
Go to our webpage, Like us on Fb, and observe us on Twitter and LinkedIn.
Disclaimer: AAAS and EurekAlert! usually are not accountable for the accuracy of reports releases posted to EurekAlert! by contributing establishments or for using any info via the EurekAlert system.
[ad_2]
Source_link