The 8 Wastes: How we optimize by subtraction (and how one can too)

[ad_1]
How does your organization sometimes deal with issues—by addition or subtraction?
Many companies default to addition. If efficiency is sluggish, they add sources. If an error happens, they add oversight. Not often do they ask the alternative query—what can we subtract to unravel our downside?
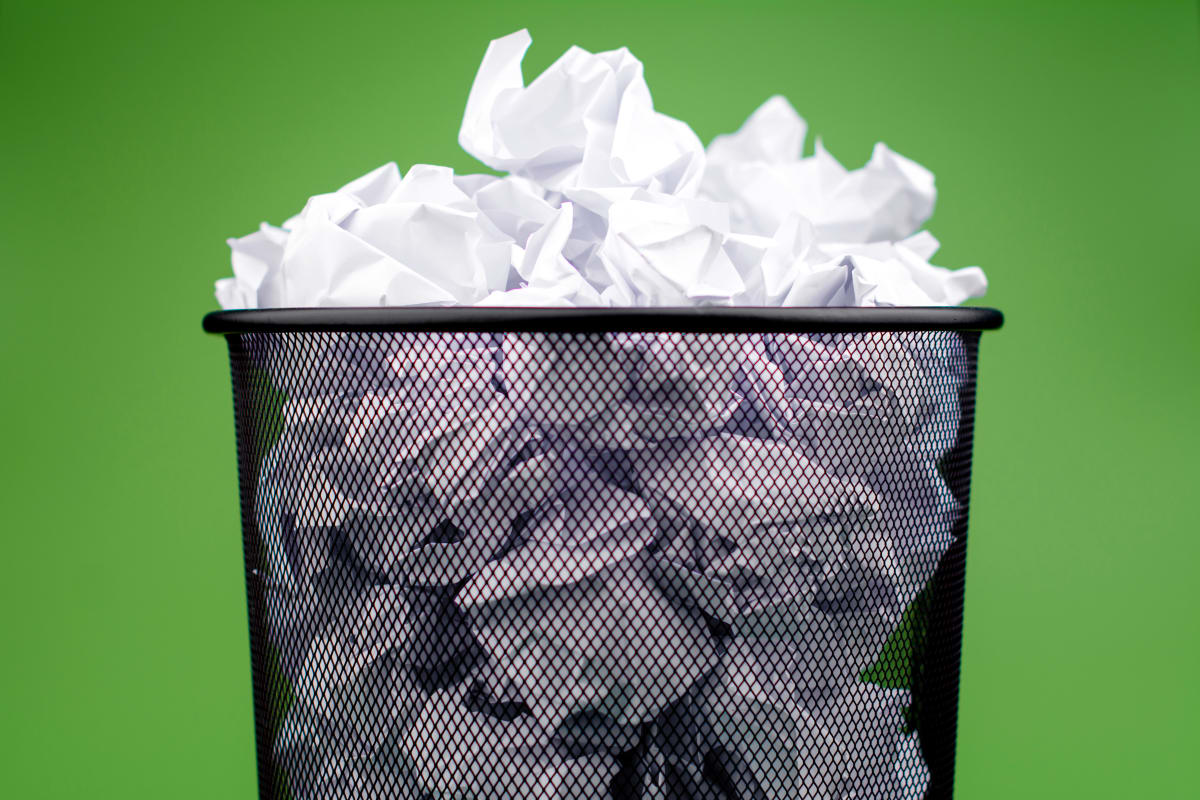
Taiichi Ohno, the daddy of Lean Manufacturing at Toyota, subtracted relentlessly. His battle on waste (or muda) revolutionized his trade and might apply to any enterprise.
Within the following article, we’ll describe The 8 Wastes and present how they’ve influenced our work at Conversion Fee Specialists. We’ll additionally:
- Redefine what “waste” means to you (and your clients).
- Clarify why 90% of your work could also be an issue.
- Set a purpose of including one productive hour a day.
For Ohno, waste was something that didn’t add worth to the client.
In case you are questioning what “add worth” means, it pays to ask a easy query. Would your clients be keen to purchase one thing individually? For instance, we would ask whether or not our shoppers would fortunately pay for our espresso breaks or bookkeeping. We doubt it—wonderful although our shoppers are. They worth the expansion we ship. That’s it. The opposite issues could also be vital to us—principally the espresso—however they add no direct worth. From Ohno’s perspective, they’re waste.
Lean companies scale back waste obsessively to allow them to deal with work that clients are keen to pay for—and income develop accordingly.
How a lot of your exercise is waste?
Lean consultants estimate that 90% of enterprise exercise is waste.
That’s not a typo.
A few of it—generally known as Sort One waste—is unavoidable. This would come with security checks on a manufacturing line or the work corporations should do to pay their taxes. You might be able to streamline Sort One waste, however you’ll by no means escape it.
Then there’s the remainder. The overwhelming majority of waste—generally known as Sort Two—is described by the seven wastes that Ohno recognized (and an eighth added later).
The 8 Wastes of Lean (with a CRE twist)
Though Ohno developed his concepts for manufacturing, we’ve utilized them to ourselves (and our shoppers) with nice outcomes:
1. Movement
We’ll at all times love this cartoon from Gary Larson of The Far Aspect. It’s additionally an important reminder of movement waste.
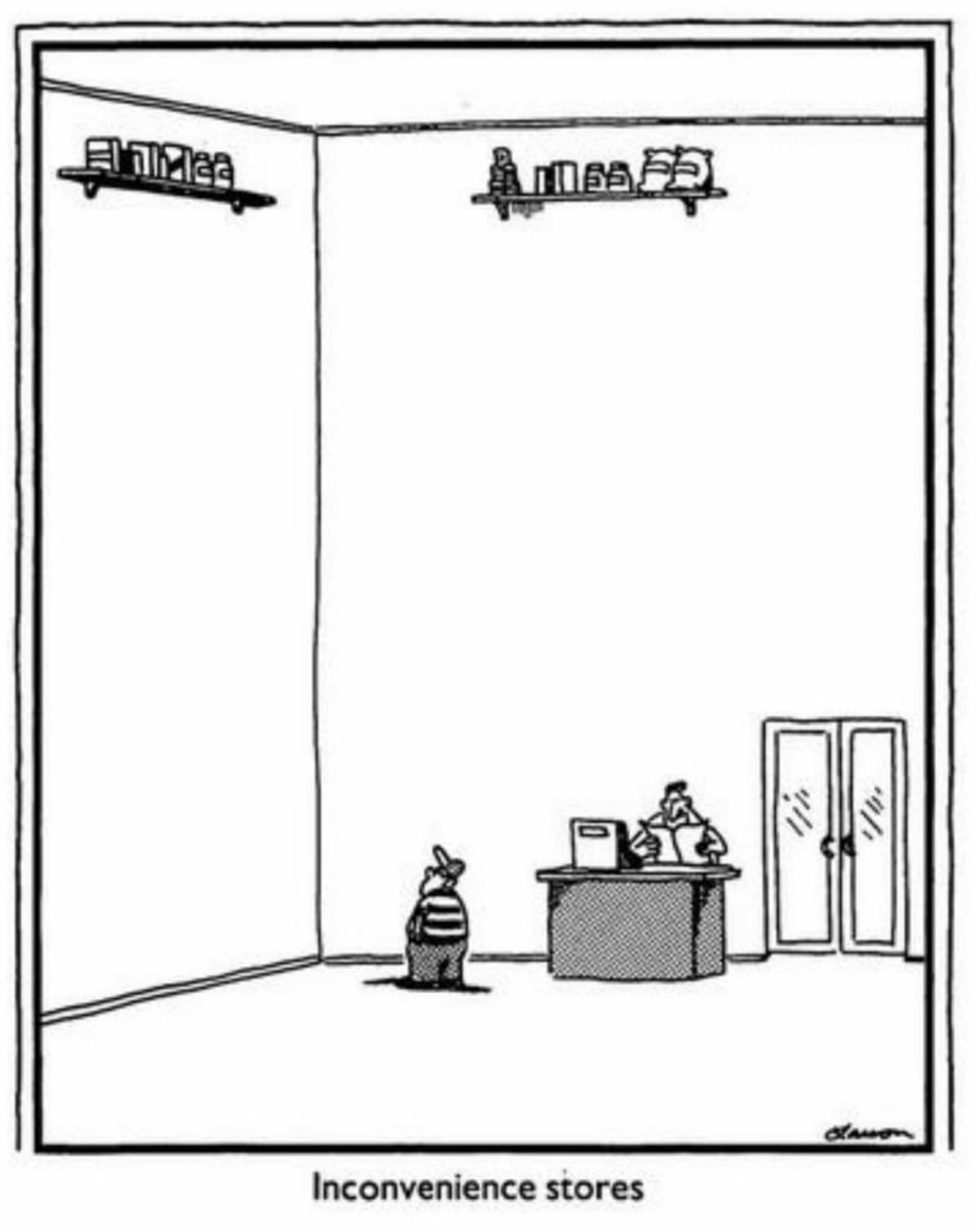
Movement waste is the surplus motion of individuals (and even the elements of individuals). Easy examples would come with having the espresso beans too removed from the grinder or requiring a buyer to navigate infinite app menus.
- We continuously streamline our workflows, eradicating extra steps and movement. See some examples in our article on How we handle our private flows.
- Likewise, we’ve delivered many wins for shoppers by eradicating extreme steps of their shopping for funnels.
- We’ve subtracted a ton of extra movement by being a distant firm since 2007. Our group members dwell the place they want and attend all their conferences on-line. (For recommendation on how one can run an environment friendly distant firm, see our Infinite Supervisor collection.)
2. Ready
Ready is a delay that leaves somebody (or some course of) idle. Apparent examples embrace a gradual load time on an online web page or a buyer on maintain at a name heart.
- To scale back ready—particularly with a group unfold the world over—we’ve constructed Conversion Fee Specialists as a community of extremely optimized flows. For every part we do—from including checks to our Wins Database to creating shopper video testimonials—there’s a Google Doc movement that anybody can observe.
- No course of can transfer sooner than its slowest stage (the bottleneck), so we use the instruments and methods of the Concept of Constraints to “break” our bottlenecks.
- The second side, in fact, is having the best group. Conversion Fee Specialists runs in accordance with Concept Y. We rent nice people who find themselves entrepreneurial by nature and powered by Daniel Pink’s “three noble motivators”: mastery, autonomy, and goal. Self-motivated individuals don’t wait to be pushed, prodded, or instructed what to do. They act. Our job is to offer them the instruments and help they want and allow them to work.
3. Overprocessing
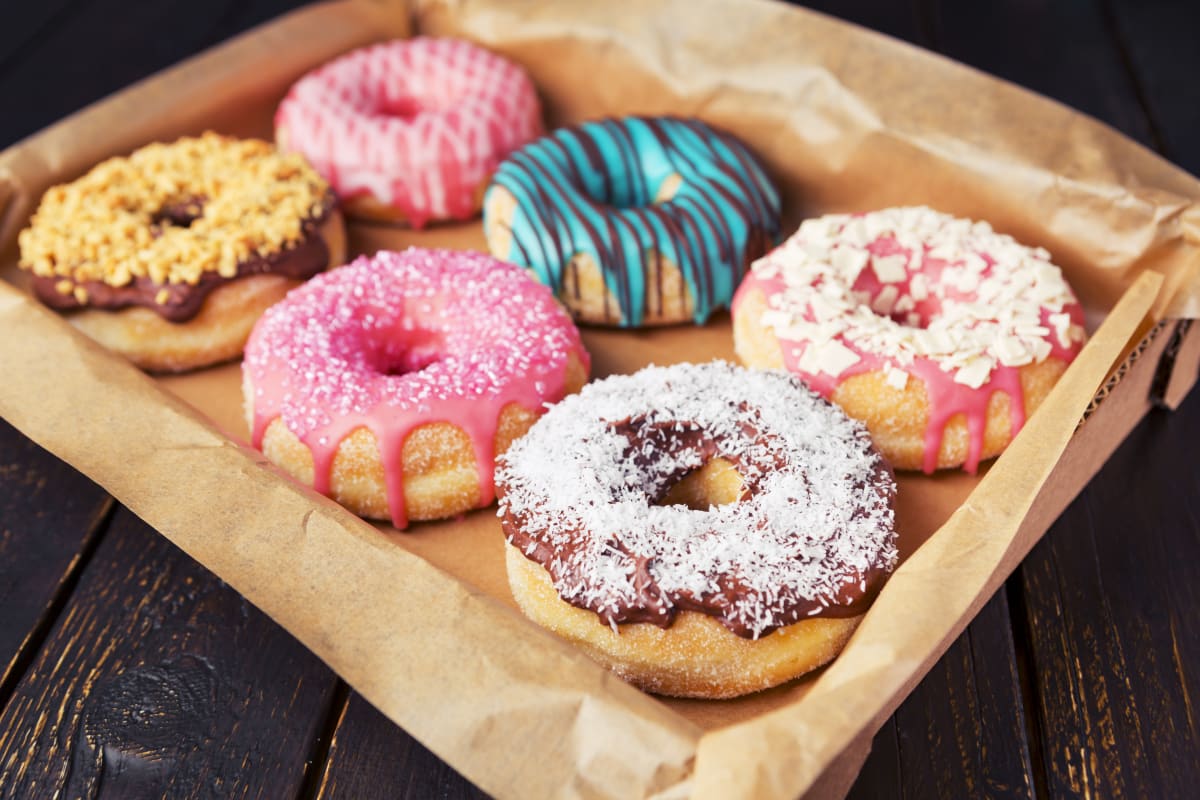
Overprocessing is further work that provides no worth for patrons. In case you’ve ever been copied on an irrelevant e-mail thread or requested to create an pointless web site account, you’ll perceive this sort of waste.
- The nice evil of overprocessing is duplication. As we wrote in our article, Duplication is evil, this concept is one among our most beneficial. “Each time we have now violated it, we have now ended up in a world of ache. (And we have now seen many corporations which have been damaged by violating it.)”
- We continuously tweak our flows to cut back processing time. For instance, our Guidelines for Holidays asks group members to let others know after they’ll be away and who’s masking their work. These emails was written “by hand,” however that was overprocessing. We now have a template embedded within the Google Doc and a one-click button to create the e-mail. As a substitute of typing an e-mail, we hit the button, fill within the blanks, and press ship.
- Martin, our CEO, was lately denied a cup of tea at a contemporary assembly house as a result of the boiling water faucet was offline… actually. It wanted Wi-Fi to work, so when the Wi-Fi failed, so did the tap! Beware. Overprocessing will get in all places.
4. Overproduction
Overproduction is creating greater than you (or your clients) want. Easy examples may embrace stockpiling vehicles that nobody has purchased or printing 1000’s of selling brochures as a result of “it’s cheaper to do a giant batch.”
- Our success rests on working profitable checks that develop a shopper’s enterprise. That sounds easy, however the big “universe” of attainable checks makes this work ripe for overproduction. To keep away from this, we do deep analysis, concentrating on the problems and checks most certainly to ship big wins. In impact, we begin each engagement by making a blueprint for enormous progress.
- Our ebook, Making Web sites Win, is a #1 Amazon bestseller in 15 classes. We frequently give hardcover copies away free of charge, however that doesn’t imply we have now stacks of them cluttering anybody’s workplace. We print small batches and ship them immediately from our companions all over the world.
- To be honest to the assembly house talked about above, boiling water taps are an important thought after they work as a result of they solely boil the water that’s wanted. Boiling extra water, against this, is a typical instance of overproduction.
5. Extra Stock
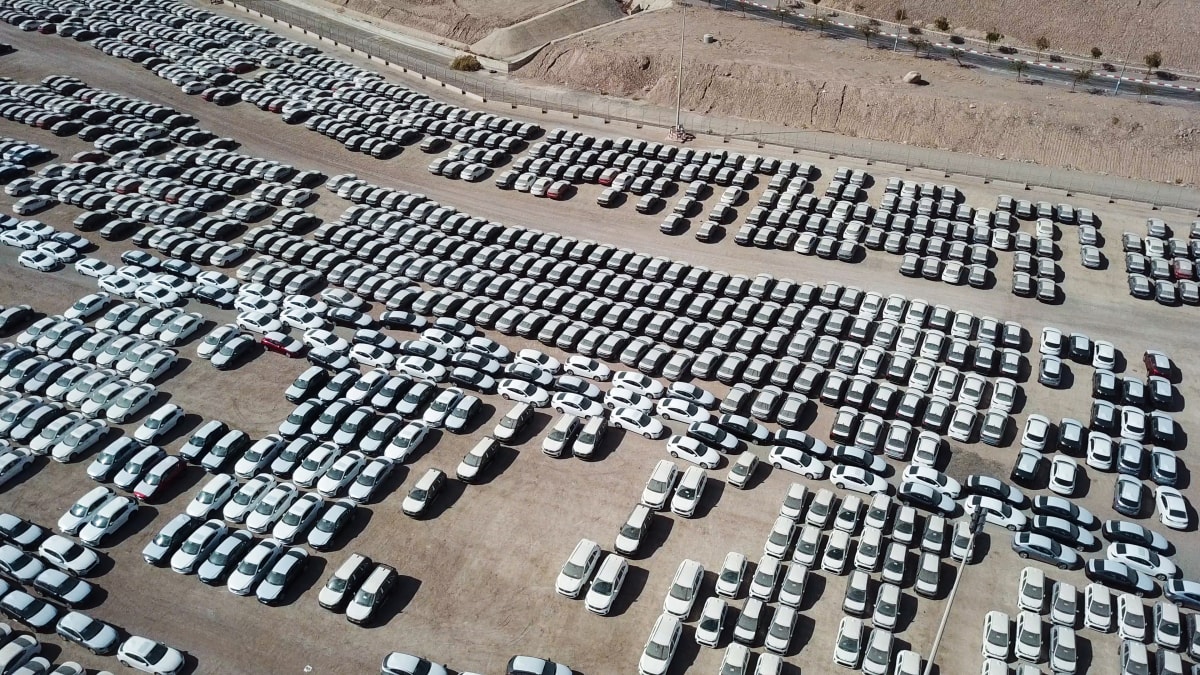
Extra stock is a consequence of overproduction. In case you’ve constructed unsold vehicles or printed low-cost brochures, it’s a must to waste time and house to retailer and handle them.
- In case you’ve learn our piece on how the world’s greatest corporations construct unbeatable focus, you’ll know that we scale back stock by limiting work in progress. This text—to take one instance—is simply being written as a result of it’s been “bought” to the content material group. It’s moved into our manufacturing movement and has a scheduled date for publication. No waste.
- Though we don’t have a lot bodily stock, it’s stunning how simply work can get “misplaced” or confused inside digital methods. Once more, see our article on the evils of duplication to grasp points this will trigger—and how one can repair them.
6. Defects
Defects gradual every part down. In case your brochures have a typo they have to be reprinted. If vehicles come off the manufacturing line with defects, they have to be mounted, scrapped, or recalled. It’s far sooner (and simpler) to get issues proper the primary time.
- We make intensive (some may say obsessive) use of flows and templates that decrease errors. For instance, right here’s a small a part of the guidelines we use earlier than sending an e-mail to subscribers:
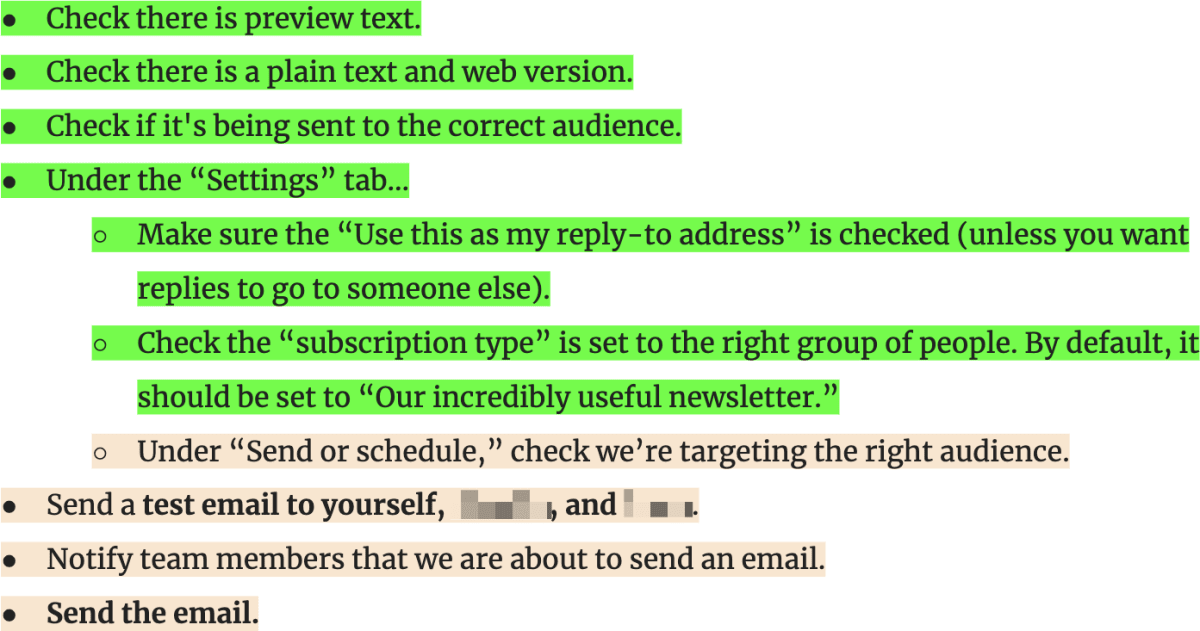
- Likewise, we purpose to reduce defects that happen over time. That’s why we write “evergreen” articles that shall be priceless for years to return. This text received’t “rust” or fall old-fashioned… at the least not till Wi-Fi boiling water taps change into bulletproof.
7. Transportation
Transportation is the product model of movement waste. Examples may embrace shifting vehicles from the manufacturing unit to the dockside, or transport brochures printed in London to be used in New York.
- We don’t have many merchandise to maneuver, however we do gather, share, and analyze so much of knowledge—every part from uncooked statistics to very large video information. To scale back our “transportation” waste, we deliberately decrease our platforms and software program stack. It’s simple to get distracted by shiny new options, however each integration or extension has a price. Our first precedence is getting the info to the place it must be, as effectively as attainable.
8. Unused expertise (or worker potential)
This closing waste was added after Ohno’s time, as lean pondering started to unfold. It’s a easy concept that’s simply missed. Most individuals are able to greater than we understand—and we waste that potential at our peril.
- We frequently use a course of referred to as Buffet delegation to seek out work that fits the talents and pursuits of latest group members, as a result of they’ve a greater thought of what they’re greatest at than we do.
- It helps, in fact, should you rent the sort of internally-motivated individuals we talked about above. At Conversion Fee Specialists, we have now a doc that tells our group what it takes to get promoted. (In case you are , we’ve written an identical article about how one can receives a commission far more.) In case you rent the perfect individuals, it pays to get out of their approach.
Why each second issues
For Taiichi Ohno, each second mattered. Each pause, mistake, or stockpile was a possibility to enhance. His method can sound obsessive till you perceive the context.
Ohno was working in post-war Japan. At the moment, their productiveness was solely a fraction of their American rivals, and Toyota feared that their trade may quickly collapse fully. Ohno’s first purpose for every employee was one “productive hour” per eight-hour shift. Though he accepted that some “waste” was inevitable—even crucial—he noticed its discount as vital to the corporate’s survival.
And a “productive hour,” in fact, is just not about explaining a trip or preventing with a scorching water faucet. It’s making nice vehicles or boosting shopper revenues.
It’s doing the work that clients actually worth.
In case your efficiency is sluggish, don’t add sources, ask what friction you possibly can take away.
It doesn’t matter what your organization does. In case you can constantly take away one hour’s waste from a employee’s day and change it with productive work—every part modifications.
How a lot did you want this text?
What’s your purpose immediately?
1. Rent us to develop your organization
We’ve generated a whole lot of hundreds of thousands for our shoppers, utilizing our distinctive CRE Methodology™. To find how we will help develop your enterprise:
Schedule your FREE technique session
2. Discover ways to do conversion
Obtain a free copy of our Amazon #1 best-selling ebook, Making Web sites Win,
really useful by Google, Fb, Microsoft, Moz, Econsultancy, and lots of extra trade leaders. You’ll even be subscribed to our e-mail publication and notified each time we publish new articles or have one thing fascinating to share.
Browse a whole lot of articles, containing a tremendous variety of helpful instruments and methods. Many readers inform us they’ve doubled their gross sales by following the recommendation in these articles.
Obtain a free copy of our best-selling ebook
3. Be part of our group
If you wish to be a part of our group—or uncover why our group members love working with us—then see our “Careers” web page.
4. Contact us
We assist companies worldwide, so get in contact!
© 2024 Conversion Fee Specialists Restricted. All rights reserved.
[ad_2]
Source_link